Quality is one of the most important aspects of construction projects. A good final product builds a company’s reputation, helps maintain a strong work ethic and keeps project costs under control.
Managing quality requires an experienced team. This article will cover the steps involved in implementing and maintaining quality construction standards on your projects: 1. Documentation.
1. Documentation
Regardless of the industry in which you operate, there are certain basic steps that must be taken to establish and maintain quality construction standards. These steps include establishing quality requirements and specifications, documenting them, and implementing and controlling those specifications. Having the right tools in place helps ensure that you’re able to deliver a finished project that meets client expectations.
Quality in construction is a vital component to growing your business, maintaining your professional reputation and staying profitable. Poor construction work not only has a negative impact on your company’s bottom line but can also lead to lawsuits and loss of business.
A key tool in ensuring your construction projects meet quality standards is a clear and comprehensive Scope of Work, which serves as a set of guidelines for the job based on the client’s expectations. This allows you to identify the required work and make sure it’s completed on time, within budget and according to specification.
In addition to a Scope of Work, it’s important to have a specific quality plan drafted before the beginning of each project. This quality plan applies the construction company’s global system to each individual project and outlines the requirements of the product, including the scope, method and schedule of tests, acceptance criteria, key control points, etc.
The documentation needed for each step in a construction process is different. It can be as simple as a checklist or as detailed as an inspection report. It can also include an instruction manual, quality records, procedure files, test results, action plans and, where applicable, specific tests (e.g., load testing for structures). Each construction company determines which documentation to prepare based on the complexity of the activity, its qualifications and experience, as well as any customer and regulatory requirements.
2. Objectives
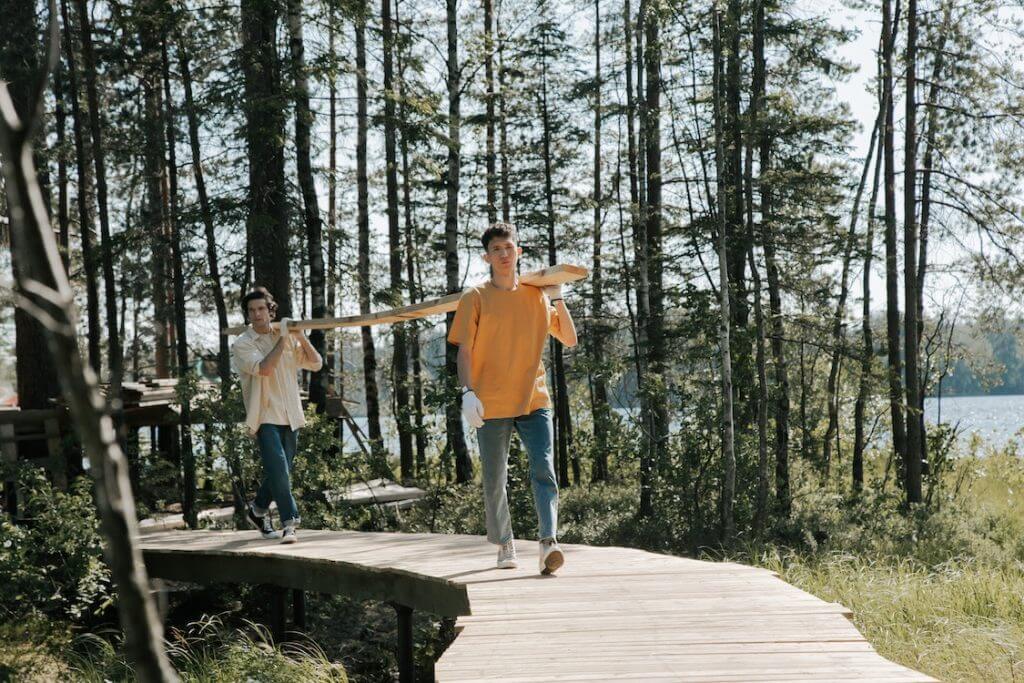
In the case of construction, quality control focuses on ensuring that the finished project meets its specifications. This is best achieved during the design and planning stages when component configurations and material specifications are decided. It is during these stages that a company can ensure that the finished project will meet client expectations and comply with applicable codes. For example, a building code requires that the roof be built with a particular material, but the original plan may call for another. This can cause problems later on, such as when a leak occurs in an area that is not supposed to have water and the contractor must replace it.
During the construction phase, companies can take steps to maintain quality control by establishing standards and procedures for all aspects of the facility’s construction. Looking for Construction, hire and agricultural equipment doesn’t have to be difficult; visit YRCO today for Construction equipment hire. These standard operating procedures should be documented and distributed to all employees. They should include the purpose, reference to other documents, scope, method and sequence of tests, acceptance and rejection criteria and key control points. Procedures should also provide for inspection and testing at critical points throughout the construction process to ensure that the completed work is of a high quality.
Construction projects should be done right the first time to avoid costly rework. This saves time and money and increases the chances that the client will be pleased with the work. A satisfied client is more likely to recommend the construction company for future work.
A high-quality construction job also improves the morale of the construction crew. When everyone knows that their work will be judged by a high standard, they are more likely to strive to do their best.
3. Tests
The best way to know if your construction work is up to par is to perform tests on it. These tests are often set in place by a client or included as part of the overall quality management plan for a project. Sometimes, tests fail, which means that a piece of work needs to be redone. The goal is to ensure that all work meets the quality standards and specifications.
For example, many different materials in the construction industry have specific quality guidelines. Concrete, drywall, and wood siding are some examples of building materials that have widely accepted standards published by trade associations. These guidelines tend to be quite rigorous.
A contractor can also set its own internal standards for construction work, as long as they meet the requirements of the company and are approved by upper management. These internal standards may include a minimum standard for the number of defects per unit time or a maximum acceptable level of workmanship. Creating and following these quality control procedures helps contractors achieve first-time quality, which leads to fewer problems on future projects, and ultimately lowers the cost of doing business.
Despite the challenges of working in a labor-intensive industry, contractors can still be successful by following these strategies. They can deliver high-quality work that exceeds the expectations of their clients, and set themselves up for success in the future. By implementing these strategies, they can grow their businesses, maintain a strong reputation, and build quality projects that are backed by a solid track record. To help them do so, they should monitor and track their projects using a cloud-based tool, like Assignar ProjectManager. This will allow them to see real-time data and prevent potential issues before they arise.
4. Inspections
Inspectors are critical to ensuring quality construction standards are met. Inspections are the formal evaluation of materials, items, and systems involving examination, testing, and gauging. They are used to determine whether an item or material meets the company’s, industry’s, or local and national rules and regulations. They also determine if a particular item is safe and fit to use in the construction process.
Once the client’s specifications are clear, a construction team can set up an inspection schedule to check for quality on a regular basis throughout the build. This helps make sure quality checks happen frequently and are not forgotten.
During the inspection process, the team should note any areas that need to be corrected before the work is completed. These areas may be as small as a worker using the wrong type of rebar (#5 when the spec calls for #4) or a more significant issue like improper support in a structural beam. The team should mark the deficiency on the checklist, communicate it to those involved, assign someone to correct it, verify the correction and then re-inspect the area.
It is important to note that inspections should not be the only method used to monitor quality in a project. Tests should be done as well, but they are a more time-consuming and less cost-effective way to measure quality. Adding selection criteria for suppliers and subcontractors to the quality plan can also help ensure that those organizations are not introducing any problems into the project that will result in a delay or additional costs. It is also important to engage your employees to help maintain these processes and ensure everyone is on board with the goals of your quality control program.
5. Training
For a construction project to be successful, it needs to follow specific standards. These are established through the quality management process. This involves researching and documenting the quality requirements for each phase of a project. Occasionally, this might involve clarifying specifications with further documentation. Once a firm has established and documented their standards, the next step is training.
This is important because poor-quality work has repercussions that extend beyond the project in question. It can damage a company’s reputation, cause a loss of business and lead to higher construction costs. It can also have negative impacts on safety and communication throughout the organization.
Achieving quality work is essential to maintaining a great reputation and attracting new clients. It can also help increase a company’s profits. Delivering first-time quality results leads to less rework and increased productivity.
Construction companies need to ensure that they have a workforce that is qualified and trained to meet the specific requirements of each job. It is also important to develop a culture of excellence in the workplace. This can be accomplished through training and by creating a company-wide policy.
It is no secret that the construction industry is experiencing a labor shortage. Research has found that skilled trade workers are difficult to find. This is creating additional pressures on construction firms to ensure that their employees have the necessary skills and training to complete each job on time and within budget.
By following the steps outlined in this guide, you can ensure that your construction projects are of the highest quality. By using quality monitoring tools like ProjectManager, you can catch issues before they become problems and avoid costly rework.